Page 3 of 4
Re: Where to have welds tested?
Posted: Mon Jan 14, 2013 11:21 pm
by Maxthegardener
So the essence of the story is??
Re: Where to have welds tested?
Posted: Tue Jan 15, 2013 1:08 pm
by TattooLeeRoy
I think it came down to- practice and destroy welds until you are confident, because the various non-destructive inspections are not neccessarily accurate with the type of coped and mitered joints involved in chopper frames.
Re: Where to have welds tested?
Posted: Tue Jan 15, 2013 2:37 pm
by Maxthegardener
Well said!!

Re: Where to have welds tested?
Posted: Tue Jan 15, 2013 9:51 pm
by TattooLeeRoy
Thank you.
Re: Where to have welds tested?
Posted: Sun Jan 20, 2013 1:24 am
by railroad bob
TattooLeeRoy wrote:I think it came down to- practice and destroy welds until you are confident, because the various non-destructive inspections are not neccessarily accurate with the type of coped and mitered joints involved in chopper frames.
That's right, in a nut shell, but sometimes it helps folks understand better if you provide a clear reason
for your opinion. Sometimes just verbalizing something helps ME have a better understanding of it.
I used to think if I built a frame I would have some inspection done, or do it myself, depending on where I was working and my resources.
I've come to understand, it isn't necessarily the best path for having confidence in what you build, the best way to have confidence in what you build is
to be knowlegable and confident about your skills and methods.
Re: Where to have welds tested?
Posted: Sun Jan 20, 2013 1:34 am
by railroad bob
Re: Where to have welds tested?
Posted: Sun Jan 20, 2013 5:28 pm
by gww25
This is actually a great thread and I'm sorry I missed it. In the real world having your welds inspected by either x-ray or magnaflux will only tell you a few things about the nature of the 'bead' and embedment into the native materials. It will not tell you anything at all about the strength of the 'joint' and this is a point that a lot of people don't understand. A weld is just a way to join two pieces of metal and in most cases the strength of the weld is about twice that of the parent materials. The strenght of the joint or connection itself however is a result of the geometry of the adjoining pieces of metal and the overall direction of stresses up and thru those joined parts. In the real world welds, even crappy welds, seldom fail. The use of gussets isn't to help in strengthing the weld joint but to create a path for the overall stresses in the frame to be more evenly distributed over larger areas. The faiure shown in the first photo is classic and very very typical. The tubing itself failed due to several possible reasons. One is that the tubing was high-tensil steel like 4130 or 1026 DOM, the second was that the tubes were 'plumbing pipe' and the third was that the tubing was exposed to excessive heating during fabrication. A forth factor was the 'hard-spot' created by the poorly designed gusset laying right on the tube centerline.
Don't worry about having your welds checked. Weld up some test joints and beat them with a sledge hammer. This is about the only test you need to do.
Re: Where to have welds tested?
Posted: Thu Feb 14, 2013 10:38 pm
by justin caise
Wow! Awesome stuff here.
Well the question was truly about verifying my skills before I set out to build my own frame(s) and it had been answered more than sufficiently. Great info and knowledge shared.
You know... this looking for “authoritative testing” may have just been another attempt of mine to procrastinate.
I have envisioned beating and cutting test pieces for inspection and that certainly sounds like more fun. But also, more - honest, or something.
“… [testing] isn't necessarily the best path for having confidence in what you build, the best way to have confidence in what you build is to be knowledgeable and confident about your skills and methods.”
TIG welded a bunch in my twenties but it was sheetmetal and autobody and, hey, wait a minute... the roll bars in handcapped van toppers, and such which were rectangular steel tubing at least .120 wall.
So for me as well as for so many others the trusting of my welding will be the jumping off point. That, sort of, rite of passage into manhood. Upping the ante usually creates the motivating fire, anyway.
So, about frame building, I’ve studied for a while, gathered tools and info, and I’ve recently entered what I’d consider the practical phase of my learning where I’m putting power to metal as it were.
Here is my first test joint using a notcher. I bought small quantities of DOM specifically for learning while I pull together other resources (money/more tools/time).
My bender isn’t finished yet but I’ll probably waste a boat load of conduit teaching myself to use it when the time comes. Anyway – it’s winter, the garage is cold, and I’m broke.
http://www.weldingtipsandtricks.com/tig ... -bike.html about bicycle frames but similar, perhaps. For you to enjoy.
Re: Where to have welds tested?
Posted: Fri Feb 15, 2013 10:42 pm
by railroad bob
Great fit up there... That is a huge part of a good weld
Oh, and don't forget the
Principle of the Seven P's...
Proper
Prior
Planning
Prevents
Piss
Poor
Performance..
Looks like you are already using that principle.
Re: Where to have welds tested?
Posted: Fri Feb 15, 2013 11:04 pm
by hansgoudzwaard
Looks nice.
Check "Irish" on this site.
I remember when he did his first frame.
Right into it now.
Re: Where to have welds tested?
Posted: Tue Nov 12, 2013 12:56 am
by railroad bob
hansgoudzwaard wrote:Maybe this will work.
NEK1.JPG
NEK2.JPG
This is a really good looking gusset design, very smooth, and NOT on the tubing centerline.
I would feel safe using this on my own bike.
I have been doing some PT inspection today, and took a few pix to share the process...
Re: Where to have welds tested?
Posted: Tue Nov 12, 2013 1:30 am
by railroad bob
This item being inspected is a 48" x 48" split tee, welded to the 48" Alaska Pipeline while still in production.
The tee is top and bottom halves fit to the mainline. The mainline pipe thickness is 0.562 wall.
The welding procedure for the groove weld on the longitudinal axis specified 8018 rod, 225F minimum preheat.
This pipe falls under DOT regulation, so the welders all have to have recent certifications to perform welds on it.
Rod size for root and hot pass is limited to 3/32 or 1/8. Fill and cover passes can be 1/8, 5/32 or 3/16 rod.
The welds are 48" long, and require 2 welders at each one. There were about 30 passes on the weld I inspected today.
After the run-off tabs are removed and smoothed, I let the metal cool to ambient temperature, and performed PT inspection
using liquid penetrant, solvent and developer.
Here is the sequence:
1. Visual acceptance of the completed weld.
2. Clean with solvent and lint free rags. Let air dry for a couple minutes so all trace of solvent is gone.
3. Apply liquid penetrant. It comes in a spray can (see below), but I use a brush so there isn't as much cleaning to do.
The penetrant has to "dwell" for a minimum of 10 minutes (longer if the temp is cooler) to allow the pentrant to use capllary action to enter any voids or cracks.
4. Use a rag to remove excess penetrant. I sue a dry rag first, then I use a rag sprayed with solvent. DO NOT spray solvent on the item as it might wash solvent out of any indication. Wait a couple minutes again.
5. Spray developer on the location carefully, too much or too little is bad. Let it dwell same as the penetrant.
Inspect the surface while the developer is going thru the dwell period.
6. After the dwell period is completed, look for rejectable indications. Not all indications are rejectable, some are considered non-relevant ( a small pocket between passes for instance). Porosity would be rejectable to API 1104, which is what code was specified for this work.
One of the pics below has pinhole porosity.
We'll be doing a girth weld tomorrow. I'll try to get some more complete pix.
Re: Where to have welds tested?
Posted: Tue Nov 12, 2013 1:36 am
by railroad bob
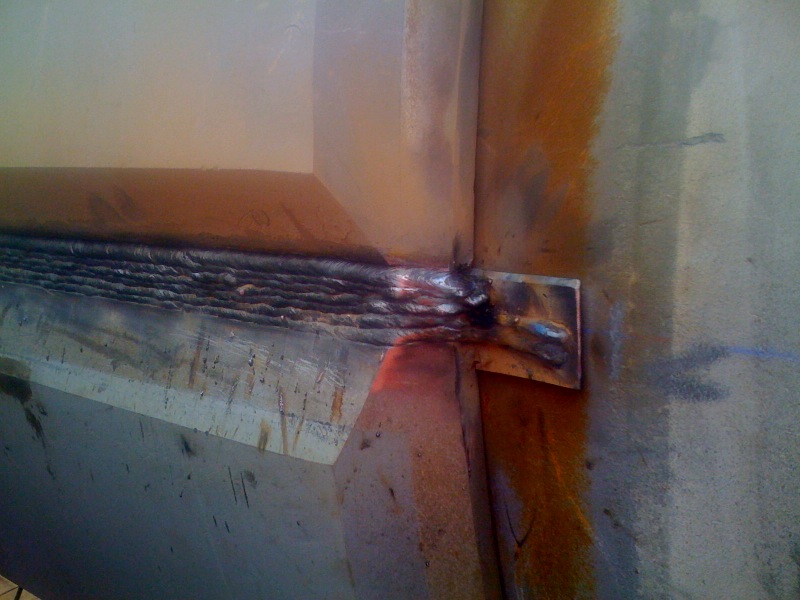
- SplitTeeRunOffTab.jpg.jpg (117.22 KiB) Viewed 6587 times
Run-off tab. Used so the weld stops can be removed. Welds stops and starts are notorious for containing or
trapping porosity or slag.

- Split Tee Long Seam.JPG (120.86 KiB) Viewed 6587 times
The completed weld after run-off tabs are removed
Re: Where to have welds tested?
Posted: Tue Nov 12, 2013 1:44 am
by railroad bob
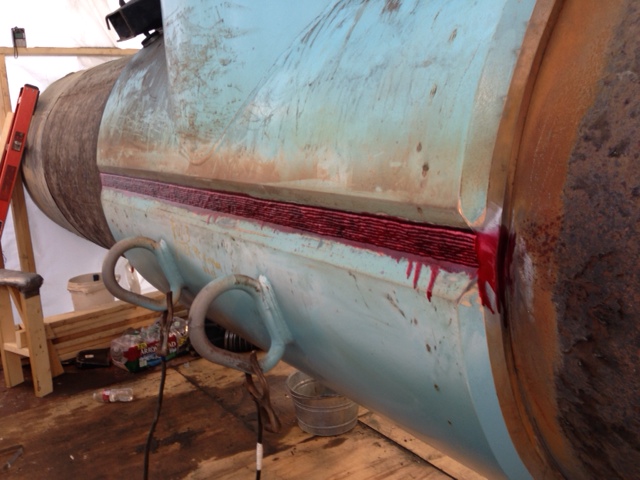
- Split Tee with PT on Weld.JPG (113.29 KiB) Viewed 6587 times
Weld after PT is applied

- Split Tee Clean PT.JPG (108.09 KiB) Viewed 6587 times
Cleaning the excess PT off weld

- Split Tee clean solvent.JPG (117.19 KiB) Viewed 6587 times
Cleaning weld with solvent after dry rag
Re: Where to have welds tested?
Posted: Tue Nov 12, 2013 1:50 am
by railroad bob
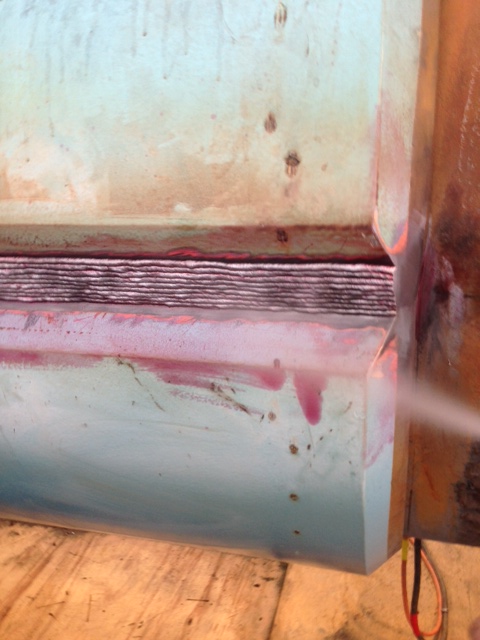
- Split Tee Spray Developer.JPG (100.85 KiB) Viewed 6587 times
Spraying the developer after cleaning off the PT

- Split Tee Developer Dry.JPG (133.69 KiB) Viewed 6587 times
The developer dries and becomes a white powder. Any excess PT will bleed thru the white and shows as a brilliant red color.