Page 1 of 1
To Die For!
Posted: Mon Jan 16, 2012 9:39 pm
by rudog
While anticipating a moment of shear horror, I decided to take a break by making another pot of coffee. Procrastinating has always been one of my strengths. While waiting on the coffee, I discovered I could kill some more time by posting what I've done this weekend. I told you I was good.
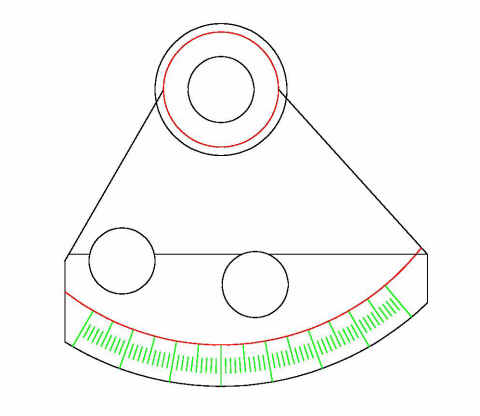
- Die1.jpg (17.01 KiB) Viewed 9189 times
I decided to build a weldment for the die that's stalled my build. It should provide up to 70* of bend. More than what I need. In any weldment, you need to have enough material to account for mis-alignment. Didn't do that. I trust on the grace of God, shear luck, and an assortment of hammers. The web came in @0.002" off center. I'll call that good (luck/grace).
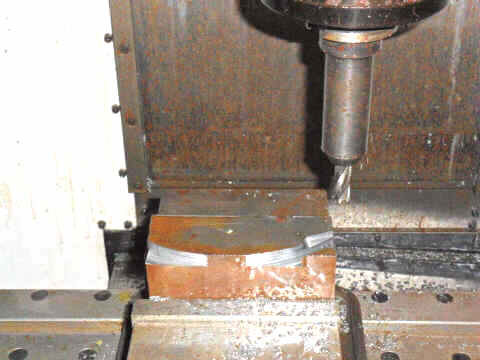
- 1.JPG (19.77 KiB) Viewed 9189 times
Re: To Die For!
Posted: Mon Jan 16, 2012 9:44 pm
by rudog
Any slack beyond that point will be machined to the hub so the profile will be centered to the hub's thru-hole. I turned a groove into the hub to center it to the block.
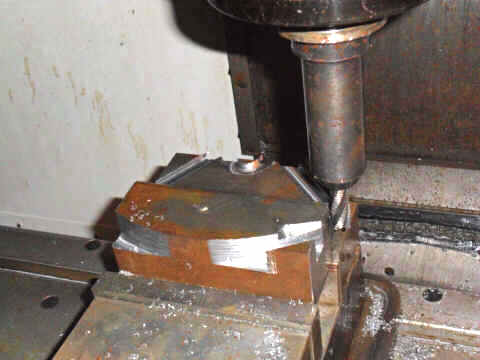
- 2.JPG (17.74 KiB) Viewed 9188 times
The f-up on the right is a problem with brain-print coordination. Everything is programed using radius. For some reason I printed the CLR as 9" dia. For an entirely different reason, I programmed a 9" rad.
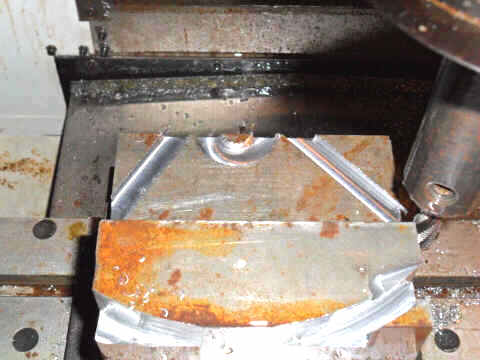
- 3.JPG (21.14 KiB) Viewed 9188 times
Re: To Die For!
Posted: Mon Jan 16, 2012 9:50 pm
by rudog
Looking at the pic below. How many of you can tell what I did wrong. I cut the profile 0.025" over to allow for a cleanup pass on the lathe. See the flat spot? That should be there! Right?
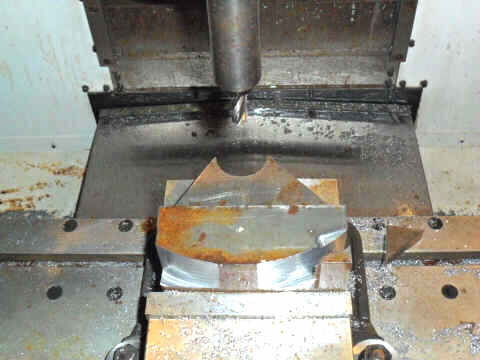
- 4.JPG (19.53 KiB) Viewed 9188 times
These are the parts prior to final weld. One c-clamp and it was pretty easy.
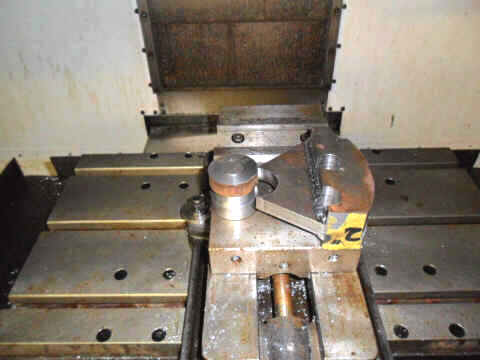
- 5.JPG (17.65 KiB) Viewed 9188 times
No matter how lucky you are, or how much you account for error, something always goes pair shaped. After cleaning the OD (center-line-radius), it came in @4.475". I forgot to account for clean-up when machining the hub c-line. It does look good though.
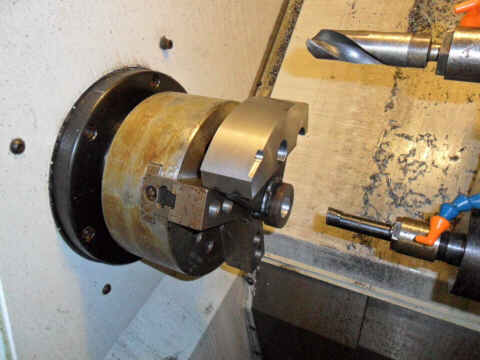
- 6.JPG (19.48 KiB) Viewed 9188 times
Re: To Die For!
Posted: Mon Jan 16, 2012 9:56 pm
by rudog
Oh, yeh! This was suppose to be a horror story. I've moved my tool as far back as I could. There's about 0.025" clearance between the insert and the part. I was hoping to do this with cutter compensation so I could squeak the profile to my sample. Oh, well! I'll just have to modify the program itself.
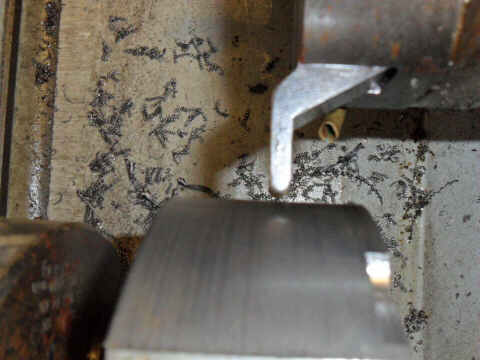
- 7.JPG (18.52 KiB) Viewed 9188 times
The moral to procrastination is that while you dread the tough stuff, the easy stuff comes to light. Round insert + round profile = 3 lines of code. And I'm not even done with my coffee, yet.
Re: To Die For!
Posted: Tue Jan 17, 2012 12:51 am
by rudog
OK! That wasn't so bad. This is the rough pass to check my dia. As expected it was small. Should have checked my insert. One side was toast.
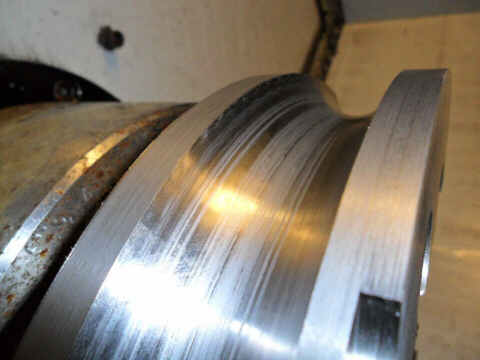
- 9.JPG (15.27 KiB) Viewed 9178 times
Several cleanup passes to squeak the dia to my sample and this is about as good as it's gonna get.
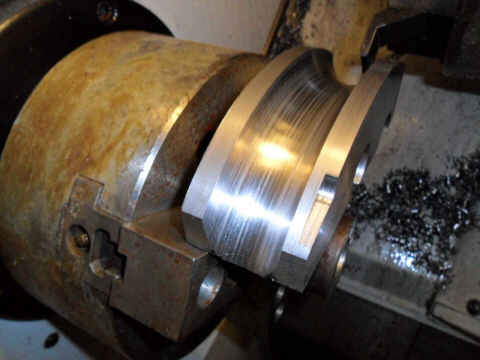
- 10.JPG (17.43 KiB) Viewed 9178 times
I still have one last pass to put the tube c-line even with the die OD. I may go a little farther also. But, I'm already into my jaws. It's a sweet sound, and I'm not using that part anyway. I may just go for it.
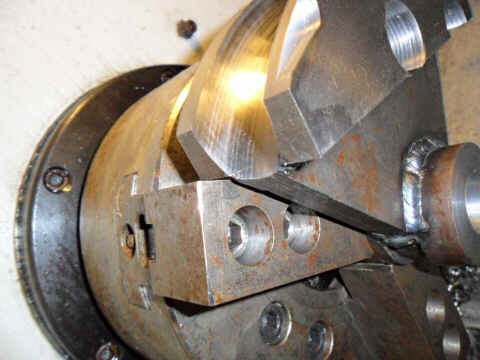
- 11.JPG (19.97 KiB) Viewed 9178 times
Re: To Die For!
Posted: Tue Jan 17, 2012 5:03 am
by railroad bob
Hard for me to tell, but it looks like you have used layers of steel plate to build the die.
I see a weld on the flat outer face of the body, is that joining two of the layers?
Re: To Die For!
Posted: Tue Jan 17, 2012 9:49 am
by krymis
good on you rudy. keep on keepin on.
Re: To Die For!
Posted: Tue Jan 17, 2012 1:12 pm
by rudog
Thanx Krymis.
Bob, the weldment is a 2x2 block, 5/8 web and 2" hub. The layering that you see is actually chip wiping from the insert. I'm not good with one-off pieces. It would take several more peices to get the speed/feed for a good surface finish. Interupted cuts on such an imballanced piece is tough.